A Concise Guide to Sheet Metal Forming
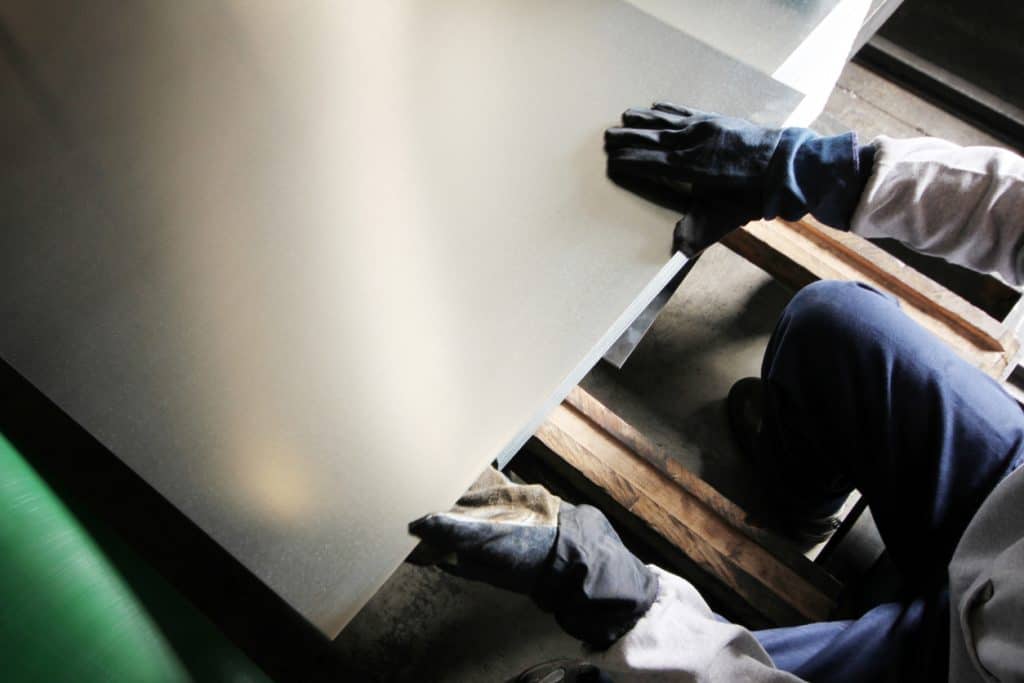
From the body of an airplane to the casing of a smartphone, sheet metal is the starting point for an endless array of products that enrich our lives. This versatile material is supplied to manufacturers as rolls or sheets of raw metal before being transformed into valuable industrial products.
Read on to find out more about the essential processes behind sheet metal forming, discover its benefits, and learn how to find an experienced fabricator for your next project.
What Is Sheet Metal Forming?
Sheet metal forming entails taking thin, flat sheets of metal and manipulating them into fully formed 3D structures. The process transforms a basic raw material into complex finished products using an array of manufacturing techniques. Conceptually, it works much like assembling a puzzle – the final 3D shape is achieved by forming many small pieces before fitting them together into one interlocking structure.
In the past, sheet metal forming was an entirely manual practice requiring specialized labor. Workers would use hammers, presses, and dies to slowly shape the sheet metal into the desired form. Today, automation and robotics have revolutionized metal fabrication, enabling far more intricate sheet metal components to be mass-produced.
What is sheet metal fabrication?
Sheet metal fabrication is the process of transforming metal sheets into various shapes through cutting, bending, and assembling. It includes techniques like laser cutting, punching, stamping, and welding to create custom metal components and enclosures. Sheet metal fabrication and sheet metal forming are sometimes used interchangeably. However, while sheet metal forming specifically refers to the processes that shape flat sheet metal into 3D parts, sheet fabrication is a broader term that includes other processes like cutting and joining to create the final product.
How Does Sheet Metal Forming Work?
Sheet metal forming leverages the malleability of metals, enabling flat metal sheets to undergo controlled plastic deformation and be manipulated into 3D shapes without tearing or compromising the material’s integrity.
The key is to use enough targeted force to coax the sheet metal to take on a desired form through bending, pressing, stretching, and other mechanical processes. However, the strain cannot exceed the metal’s ultimate tensile strength, or it will become damaged.
To keep deformation in the safe plastic zone, skilled control of parameters like the magnitude of force, speed of application, temperature, and material orientation is required. Automated systems now replicate these complex calculations to shape metal uniformly without defects. However, small-batch custom metal forming often still relies on the skill and judgment of experienced technicians.
Sheet Metal Forming Processes
There are a variety of core manufacturing processes used to form sheet metal into parts. The techniques deployed depend on the geometries and production volumes needed, as well as the formability of the selected metal. Following design for manufacturing guidelines when modeling parts also ensures they can practically be formed.
Let’s look at some of the most popular sheet metal forming options:
Bending
Bending works by inducing controlled plastic deformation in the metal to create angled forms. This is achieved by securing the sheet metal blank within a press brake and using a V-shaped punch tool to form the bend. The sheet metal is pressed between the descending punch, and a bottom die with a matching width and angle profile is cut into it. The depth that the punch tool presses down controls the resultant bend angle in the metal, up to a maximum of 180 degrees for an entirely flat form.
Laser Cutting
Laser cutting uses a high-powered laser beam focused through optics on a CNC machine. The heat from the laser locally melts and vaporizes the sheet metal to “cut” intricate patterns defined in CAD software. The process, known as sheet metal laser cutting, can develop complex geometries rapidly and accurately in metals like steel, aluminum, and titanium.
Hydroforming
Hydroforming uses highly pressurized fluid instead of traditional mechanical force to form sheet metal. The metal blank is placed between two die halves, and hydraulic fluid pressure is progressively applied. This is used to create seamless shapes like automotive space frames or aircraft wings.
Stamping
Stamping presses use rigid punch and die tooling to form sheet metal in very high production volumes. During the stroke of the press, the punch strikes and presses the metal into the shape defined by the female die cavity below it. Stamping can form deep, concave metal parts at rates of hundreds per minute, like housings, enclosures, and body panels.
Drawing
Drawing pulls sheet metal through a die opening using a mechanically actuated punch. As it passes through the metal plastically deforms to take the shape of the narrowing die geometry below it. This creates precisely formed seamless “cups” which can be further processed. Common drawn parts include ammunition casings, medical implants, and spacecraft nose cones.
What Materials Are Used in Sheet Metal Forming?
Several metals and metal alloys can be readily formed from sheet stock into finished parts. The material used depends on the properties needed in the application.
- Steel: Due to its strength and formability, steel makes up much of the globally formed sheet metal output. Everything from kitchen appliances to cars to buildings relies on steel fabrication.
- Stainless Steel: By adding chromium, stainless steel gains corrosion resistance for use in applications like industrial equipment, surgical instruments, and food preparation tools.
- Brass: A zinc and copper alloy, brass can be shaped into decorative parts without fracturing. Its gold-like finish makes it popular for musical instruments, hardware, and marine components.
- Aluminum: This metal is used in applications that need light and corrosion-resistant materials. Examples are aerospace structures, automotive vehicles, and marine applications.
What Are the Benefits of Sheet Metal Forming?
Unlike competing alternatives such as machining and casting, sheet fabrication allows the cost-effective, flexible, and rapid production of metal components. Here is a detailed explanation of the benefits:
Cost
The processes and equipment used in most sheet metal forming methods are relatively affordable. Techniques like bending and stamping employ simple dies and presses to deform sheet metal into shapes. This avoids the expensive multi-axis CNC machining or injection molding tools needed for other processes. The result is parts fabricated at high volumes with low per-unit costs.
Flexibility
A key benefit of sheet metal forming is flexibility in the geometries and applications possible. The same progressive stamping die used in an automotive plant can be repurposed and retooled to make entirely different parts. The adoption of 3D printing for shaping metal components is revolutionizing formability, offering new avenues for innovation. Due to its diverse fabrication options, sheet metal is used across industries, from aviation to appliances.
Rapid Production
Prototype parts or custom orders requiring fast turnaround times benefit from using sheet metal forming over slower techniques like casting or machining from billet. Most sheet metal parts can be formed with the single stroke of a press or strike by a hammer. At low to moderate volumes, this enables rapid production cycles to meet changing demands.
How Sheet Metal Forming Optimizes Manufacturing
Sheet metal forming integrates well with modern computer-controlled manufacturing workflows for increased speed, precision, and consistency. Digital tools empower efficient design-to-production for fabricated sheet metal components. CAD software provides detailed 3D models of parts for simulation and planning. Instructions are then automatically translated into executable code that drives CNC machine tools.
This combination of digital design and automated fabrication removes a considerable portion of the historic trial-and-error in metalworking. Every stroke of the press or pass of the laser cutter can be virtually tested before physical production, preventing wasted time or materials caused by faulty tool paths or forming errors. It also enables faster design iterations and change integration compared to manual processes.
Once optimized, automated sheet metal forming machinery can operate unattended 24/7. Robotic arms tirelessly load raw materials and form parts with absolute precision unmatched by humans. This drives high-volume production while maintaining consistent quality standards. Integrated sensors provide real-time feedback, automatically adjusting parameters like press speed and die lubrication in response to environmental changes.
Using MFG for Sheet Metal Forming Needs
As we’ve seen, sheet metal forming enables the creation of versatile, durable, and cost-effective metal components that are vital across every industry. However, transforming your innovative designs into physical products requires the help of an experienced fabricator equipped to meet your specific needs. But how do you start to look for the best-qualified, thoroughly vetted, and well-reviewed specialists?
MFG makes connecting with the best sheet metal manufacturers for your project simple and seamless. With MFG you get exclusive access to the world’s largest network of elite custom fabricators specially vetted for quality and reliability. Save time by avoiding the hassle of sending RFQs to multiple manufacturers only to later realize they can’t handle your project or meet your standards. MFG pre-qualifies them for you, Ensuring a smoother and more efficient process.
Get started now by submitting your project details for free. Within hours, you’ll receive precise quotes from MFG’s exclusive network of top-tier manufacturers specializing in sheet metal forming, putting you on the fast track to bringing your project to life.