Integrating Additive and Traditional Manufacturing to Optimize Production
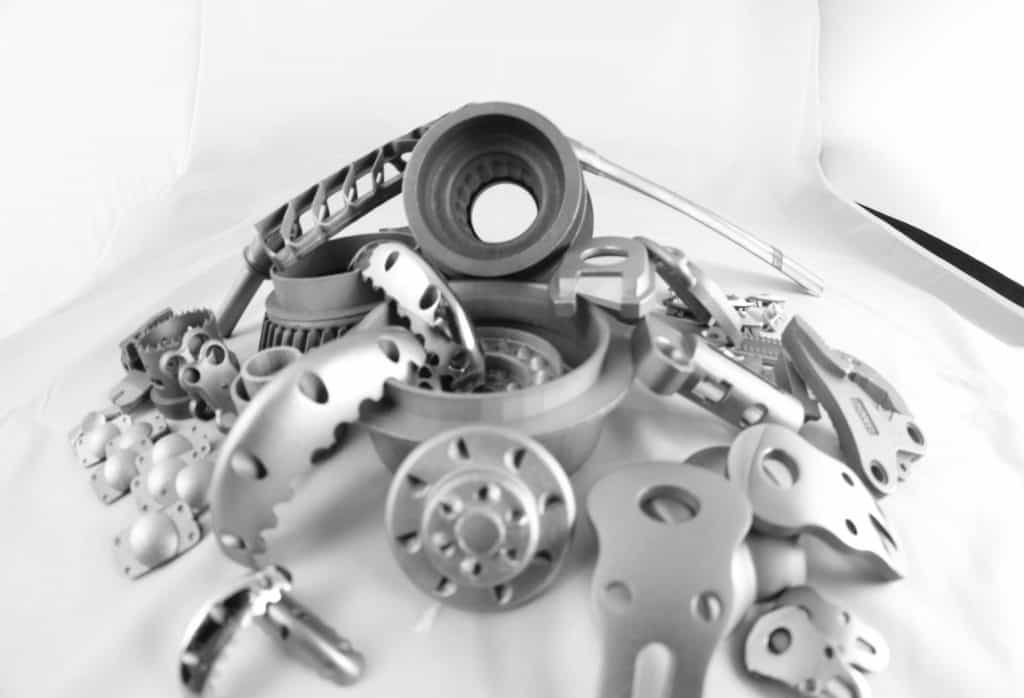
3D printing, also commonly referred to as additive manufacturing, continues to transform design and production in nearly every industrial application imaginable. This disruptive technology liberates manufacturers from the confines of traditional production processes, allowing for the creation of complex, highly customized geometries that were once thought impossible.
Despite the numerous advantages of 3D printing, however, traditional manufacturing has stood the test of time due to the scalability, precision, and material versatility offered by technology like CNC machining, injection molding, and metal fabrication. By strategically integrating 3D printing with these methods, manufacturers are better equipped to meet evolving market demands—remaining competitive, and driving future growth.
How 3D Printing Works
The 3D printing process begins with the design of an object using Computer-Aided Design (CAD) software. The design is then sliced into numerous thin layers. The 3D printer reads these files, depositing layer upon layer of material, like plastic or metal, onto the building platform, following the design instructions. As each layer solidifies, the next layer is added, until the object is fully formed. This layer-by-layer construction is what distinguishes 3D printing from traditional subtractive manufacturing processes, like CNC machining, where material is removed from a larger block to form the final object.
Key 3D Printing Technology and Materials
3D printing has evolved over the decades, leading to advancements in various 3D printing technologies. Some of the most commonly used techniques include:
- Stereolithography (SLA): This technology uses an ultraviolet (UV) laser to solidify photopolymer resin layer-by-layer, resulting in high resolution and exceptional surface quality. SLA is ideal for smaller objects, and for applications requiring precise details and a smooth finish.
- Selective Laser Sintering (SLS): Relying on powdered polymers like nylon for creating tough and temperature-resistant complex geometries, SLS technology uses a high-powered laser to fuse materials together. SLS is extremely popular, and a suitable choice for 3D prints of any size.
- Multi Jet Fusion (MJF): Developed by HP, MJF uses a fine-grained powder, typically nylon, to create parts with high density and low porosity. MJF 3D printing is an excellent choice for complex, highly detailed industrial parts.
- Metal 3D printing techniques: Technologies like Direct Metal Laser Sintering (DMLS), Selective Laser Melting (SLM), Electron Beam Melting (EBM), and Laser Powder Bed Fusion (PBF) enable 3D printing of complex geometries using metal powders, including titanium, steel, aluminum, and precious metals like gold and silver.
Understanding these techniques and their associated materials helps manufacturers determine the optimal 3D printing method based on their specific needs, whether for high-resolution prototypes, or durable, complex parts.
Redefining Traditional Manufacturing with 3D Printing
3D printing makes it possible for manufacturers to perform rapid prototyping during the product development process, as well as running small production batches with improved efficiency and cost-effectiveness. Key benefits manufacturers can enjoy include:
- On-Demand Manufacturing: 3D printing enables the production of parts as needed from a digital file, reducing inventory costs and waste. On-demand manufacturing eliminates overproduction, allowing for quick adjustments to be made to product designs according to real-time demand.
- Supply Chain Simplification: By integrating 3D printing, manufacturers can significantly reduce dependency on multiple suppliers by printing parts in-house or locally. This reduces the complexity of logistics and lowers the risk of supply chain disruption due to external factors.
- Improved Product Quality: With 3D printing, manufacturers can produce parts with a higher degree of precision, leading to a better fit and finish. This can significantly improve the final product’s quality and performance, potentially increasing customer satisfaction and market share.
- Risk Reduction: 3D printing allows manufacturers to verify designs before investing in expensive manufacturing equipment or tooling. This process can highlight potential design flaws early, reducing the likelihood of costly errors later in production. By reducing the need for upfront investment in molds and tools, 3D printing can also significantly lower the cost associated with launching new products.
This acceleration in product development can bring products to the market faster, while also allowing for the production of complex, customized parts that may not be possible through traditional manufacturing.
Industrial 3D Printing Applications
Following are just some of the diverse applications where the combined power of 3D printing and traditional manufacturing are making a significant impact.
Aerospace
The aerospace industry benefits tremendously from the integration of 3D printing and traditional manufacturing. The ability to produce complex geometries and high-performance components using metal 3D printing techniques enhances aircraft performance and fuel efficiency—especially with parts that are incredibly strong and lightweight. The combination of 3D printing and traditional manufacturing also allows for rapid prototyping, reducing design iterations, and enabling faster time-to-market for new aerospace innovations.
Architecture and construction
3D printing allows for the production of scale models in a matter of hours, improving visualization, and aiding in better design decision-making. With the combination of traditional and additive manufacturing, it’s possible to build complex, full-size structures with less materials, paving the way for more sustainable and innovative construction practices.
Automotive
Although the automotive industry relies on traditional manufacturing for most high-performance parts, 3D printing allows for rapid prototyping as well as functional parts that are lighter in weight and require less material. This is a critical advancement for an industry constantly seeking ways to improve fuel efficiency and performance while reducing its environmental impact.
Consumer Goods
The integration of 3D printing and traditional manufacturing in the consumer goods industry has brought remarkable advancements. Rapid prototyping capabilities accelerate product development, allowing businesses to iterate designs and test products more efficiently. This technology also enables greater customization and design intricacy, resulting in unique and personalized consumer goods that meet specific customer preferences.
Medical
3D printing has revolutionized the medical field, offering incredible opportunities for patient-specific care. From personalized prosthetics and implants to highly accurate anatomical models for surgical planning, additive manufacturing enhances patient outcomes and operational efficiency in healthcare. The integration of 3D printing and traditional manufacturing enables the production of custom medical devices with high precision and intricate geometries, improving the quality of life for patients.
Hybrid Production Merges 3D Printing and Additive Manufacturing
3D printing and traditional manufacturing need not be mutually exclusive; in fact, a hybrid manufacturing approach, strategically combining these two methods, can unlock significant potential and provide innovative solutions for manufacturers.
One of the key benefits of hybrid manufacturing is the optimization of the production process. Manufacturers can employ 3D printing for rapid prototyping, enabling quick and cost-effective design iterations. Once the design is finalized, they can seamlessly transition to traditional manufacturing methods like injection molding for mass production. This approach accelerates the product development cycle, reduces costs, and minimizes waste. Changes can be made digitally in the design phase, eliminating the need to physically alter expensive tooling or equipment.
Additionally, hybrid manufacturing enables the merging of multiple components into a single assembly. With 3D printing, parts that were traditionally produced and assembled separately can now be created as a single piece. This consolidation not only reduces the number of parts and associated costs but also eliminates potential points of failure. By enhancing the product’s durability and longevity, manufacturers can deliver higher-quality products to the market.
3D Printing in CNC Machining, Injection Molding, and Fabrication
3D printing is also making significant strides in complementing traditional manufacturing processes like CNC machining, injection molding, and sheet metal fabrication. Leveraging the unique advantages of both 3D printing and traditional methods, manufacturers are discovering new opportunities for enhanced design capabilities, cost-effective production, and streamlined processes.
CNC Machining and 3D Printing
CNC (Computer Numerical Control) machining is a traditional manufacturing process where pre-programmed software dictates the movement of machinery. Although CNC machining is effective for creating precise and repeatable parts, it can be time-consuming and costly for intricate and complex designs.
3D printing’s capability to create complex geometries without the need for expensive tooling has made it a viable alternative to CNC machining for certain applications. Combining both methods can also lead to a powerful synergy where 3D printing is used for prototyping and small runs, and CNC machining for large-scale production.
Injection Molding and 3D Printing
Injection molding, the process of injecting molten material into a mold, is a popular method for mass-producing plastic parts. However, the initial cost for creating the molds can be high and lead times can be lengthy.
3D printing is being used more commonly to create molds for low- to medium-volume production runs, reducing both costs and lead times. This technology also allows for the production of parts with complex geometries that would be difficult to achieve with injection molding alone.
Sheet Metal Fabrication and 3D Printing
Sheet metal fabrication is a traditional method that involves shaping flat sheets of metal into the desired part through cutting, bending, and assembling. While this method is effective for producing sturdy, metallic parts, it can be labor-intensive and restrict design complexity.
3D printing enables production of complex metallic parts with less labor and more design freedom. With metal 3D printing, manufacturers can create parts that are lighter, stronger, and more complex than those made with traditional sheet metal fabrication.
By capitalizing on the strengths of both traditional and additive manufacturing methods, businesses can accelerate product development, reduce costs, and create complex geometries that were previously impossible, while traditional manufacturing can efficiently produce large volumes of products. By merging these two methods, manufacturers can achieve greater design flexibility, faster time-to-market, and improved efficiency.