Injection Molding
MFG’s database includes thousands of Injection Molding businesses. Find your match.
Or, are you a manufacturer?
Industrial manufacturing has seen numerous revolutionary methods and processes develop over the last century and a half. Among these, injection molding has consistently been recognized as one of the most cost-effective, precise, and quality-driven solutions. Injection molding has also (to say the least!) marked substantial growth with the advent of innovative materials and technology.
Today, as the manufacturing world continues to change at a rapid pace, injection molding remains a driving force in industrial advancements, meeting growing market demands and pushing the boundaries of environmental sustainability.
What is Injection Molding?
The concept of injection molding emerged in the 1800s, and was further solidified with the granting of a patent to John and Isaiah Hyatt. These pioneering brothers introduced the concept of molding compounds, with their original patent setting the foundation for the development and widespread adoption of injection molding as a vital process—forever changing the face of manufacturing through mass production.
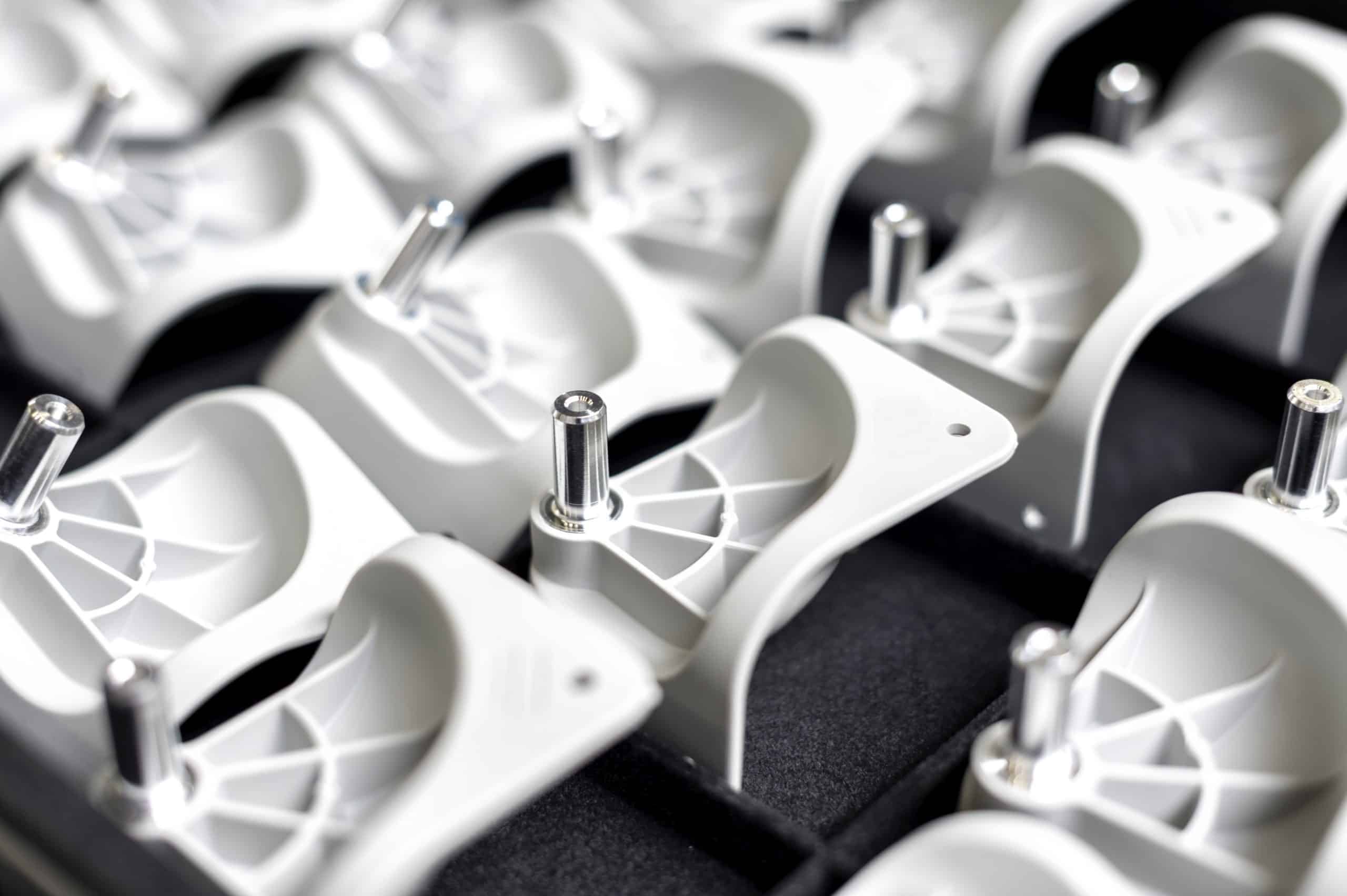
Injection Molding: Plastic Parts
Overview
Injection molding encompasses critical phases such as material preparation, mold clamping, injection, cooling, mold opening and ejection, and mold closing.
Central to this process is tooling known as the mold, composed of a stationary half (the cavity) and a movable half (the core). Thermoplastic materials are typically introduced into the injection molding machine as pellets or granules, and then heated into a molten state.
Once injected into the mold via a nozzle, the liquid material immediately begins cooling, usually aided by a circulating coolant, air in the mold, or cooling channels made for the interior of the mold. Cooling is a critical stage in Injection Molding as proper cooling determines quality in shape and mechanical properties.
Solidifying and taking the shape of the desired product, the mold opens and the part is ready to be ejected, in either a manual or automated process using either ejector pins or a robotic arm, respectively. Afterward, the mold halves close, and the cycle repeats for production of the next part. Most manufacturers will repeat the injection molding cycle multiple times to meet production demands efficiently.
Cycle times may range from a few seconds to several minutes, depending on:
- Production volume
- Complexity of parts
- Time required for each part
Manufacturers are always working harder to optimize cycle times, running hundreds or even thousands of cycles. The goal is to achieve maximum productivity, while also consistently producing high-quality parts.
How to Manufacture with Injection Molding
Manufacturing with injection molding requires a systematic approach, made up of several steps which must be followed precisely for efficient production runs—and successful results:
1. Material Preparation
Thermoplastic materials are typically used in injection molding. These materials are converted into cylindrical pellets or granules ranging in size from a few millimeters to a few centimeters. Material selection is based on industrial application requirements, considering factors like strength, durability, heat-resistance, and flexibility. During production, material pellets are loaded into the hopper, which then feeds them into the injection-molding machine.
2. Mold Design
This step is critical in determining the final shape, features, and quality of products. Part geometry, draft angles, and cooling channel layouts are also essential considerations during mold design. Many manufacturers employ computer-aided design (CAD) software to create precise metal or silicone molds that can be 3D printed on demand for customized and accurate parts.
3. Machine Setup and Injection
Before production begins, the injection molding machine must be properly prepared. This includes heating the barrel to the appropriate temperature for melting the materials, and configuring machine parameters to meet the part’s specific requirements—including injection speed, pressure, and temperature. The injected molten materials, referred to as ‘the shot,’ are then injected under high pressure to create the molded product.
4. Post Processing
Depending on the desired characteristics and requirements of the final product, post-processing may be necessary. This can include removal of excess materials, elimination of visible gate marks or spruces, and the addition of surface finishes. Some parts may require painting or assembly to complete the manufacturing process.
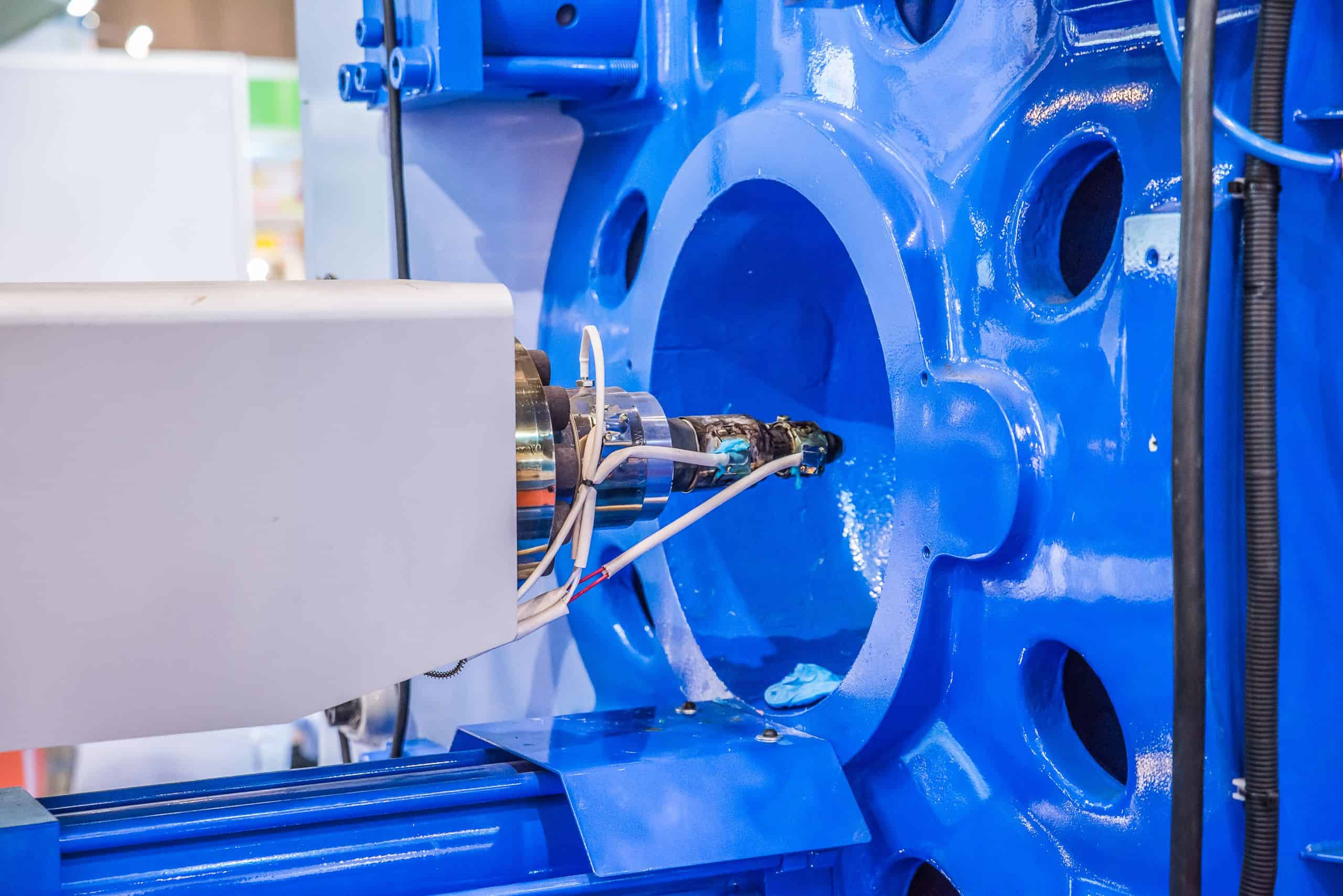
Injection Molding Machine
From preparation to post-processing, manufacturers must also maintain consistent quality control processes, ensuring excellence in parts. For success in injection molding, that means monitoring machines, inspecting parts thoroughly, and testing materials.
More advanced inspection techniques may be required too for analyzing parts as well as verifying dimensional accuracy and assessing geometric tolerances. Non-destructive testing may also be necessary to evaluate the internal quality and integrity of injection molded parts.
Get an Instant and Competitive Injection Molding Manufacturing Quote
- Easily find the custom part manufacturer your project requires
- Get instant and competitive quotes on your RFQs
- All uploaded files are securely stored on MFG and only released to manufacturers at your discretion
Note: MFG does not service the textile, jewelry, or clothing industry.

Request a Quote
Have part files ready?
Submit an RFQ in 2 easy steps.
Step 1
Upload your part file below.
Drag and drop a file here or click to upload
Oops! The file size needs to be less than 500 MB. Please upload a small file.
All files are protected by the MFG Standard NDA and are securely stored on MFG.
Step 2
Just a few extra details.
Your Contact Information
Let them know how to contact you.
All information is transmitted and stored securely. We will never sell your information.
Congratulations!
We have received your RFQ! Once accepted, we will contact you.
Hi! Did you know you can keep track of this RFQ in your MFG Community account?
Injection Molding Techniques
Manufacturers rely on different types of injection molding, all designed to serve varying project requirements. Some of these include:
Overmolding
This technique enhances the strength, durability, and aesthetics of a part, using means to add cosmetic or functional features. Overmolding is typically used to inject materials over pre-existing parts.
Insert molding
This method makes it possible for manufacturers to combine materials, like multiple plastics or plastics and metal. An existing part is inserted into the mold, and other materials are injected around the structure.
Micro-molding
This technique allows manufacturers to create extremely small parts that require intricate detailing. Micro-molding is typically used in medical and electronics applications.
Gas-assisted injection molding
Manufacturers rely on gases like nitrogen for this technique, creating hollow sections within the mold to reduce material usage and reduce weight—while also maintaining the integrity and strength of the injection-molded part.
Injection Molding Plastics
A wide variety of different plastics can be used to meet project requirements also, including the following:
Acrylonitrile Butadiene Styrene (ABS)
This material is widely used in injection molding due to its exceptional toughness, as well as resistance to impact and heat.
ABS is popular with manufacturers due to its ability to withstand high temperatures, making it suitable for applications like automotive, electronics, and consumer goods like toys.
ABS also exhibits good dimensional stability, and can be easily post-processed—allowing for additional surface finishes and customization options.
Polyethylene Terephthalate (PET)
This material offers a combination of desirable properties, including excellent clarity, high strength, and resistance to impact and chemicals.
These characteristics make PET a preferred material for packaging applications like bottles, jars, and containers for food and other products.
Polypropylene (PP)
This versatile material is widely regarded for its flexibility, chemical resistance, low density, and affordability.
PP provides excellent resistance to fatigue, moisture, and chemicals, making it suitable for various applications, including automotive parts, packaging, household products, and medical devices.
PP can be easily molded into complex shapes, and is often chosen for its lightweight nature and ability to withstand demanding environments.
Polystyrene (PS)
This material is a popular choice in injection molding to ease in processing, excellent clarity, and shiny surface finish.
PS is widely used in the packaging industry for disposable products like food containers, cups, and trays.
PS is also used with injection molding processes to create consumer goods, electronics, and healthcare products where transparency and aesthetic appeal are designed. This material can be molded into intricate designs too.
How does Injection Molding add value in manufacturing?
Injection molding has played a pivotal role in the manufacturing process, revolutionizing industries such as automotive and consumer goods. The exceptional productivity and quality associated with injection molding techniques have made the process an integral part of mass production.
The efficiency of injection molding for large volumes makes it the go-to solution for manufacturing thousands of identical components. The process enables manufacturers to scale production while maintaining cost-effectiveness, meeting the specific requirements of various industries such as packaging, electronics, and automotive.The design flexibility and precision of injection molding allow for the creation of complex and customized parts.
Injection molding also contributes to sustainability by reducing scrap and material waste. With accurate mold designs and optimized production processes, plastic waste is minimized, making it an environmentally-conscious choice. This aligns with the growing demand for eco-friendly practices, meeting the expectations of conscious consumers and businesses committed to reducing their environmental impact.
As the manufacturing industry evolves, injection molding remains a leading force, continually advancing through automation, digitization, and sophisticated quality-control methods. These developments, combined with the inherent cost-effectiveness, precision, and quality of injection molding, position the technology in a critical role for manufacturers.
The future of injection molding is as promising as its history is rich. With continual technological advancements, injection molding is poised to keep reshaping the world of manufacturing, driving sustainability, and serving the ever-growing needs of diverse industries.