Sheet Metal Fabrication
Find a sheet metal fabrication business on MFG.
Or, are you a manufacturer?
What is Sheet Metal Fabrication?
Manufacturers often obtain materials within the metal supply chain in the form of rolls or sheets. These raw materials are necessary to their own production processes, and must be transformed into valuable, industrial products through sheet metal fabrication–also commonly known as metalworking.
Industrial processes used to manufacture goods vary widely–from production of household products like foil trays to aluminum foil and heavy-duty products like fences, gates, cars, and planes. Popular techniques include bending, cutting, punching, and welding of materials to bond multiple pieces. Since metallic products have an assortment of uses, different standard fabrication steps must be sequenced to achieve the finished material.
Sheet metal fabrication involves the transformation of a nearly 2D structure, like a metal sheet, into a fully-realized 3D product. This process is similar to putting a puzzle together. The smaller pieces of sheet metal are formed first, interconnected, and then locked together securely to achieve the desired final shape. While historically a manual practice, recent industrial advancements have automated metal fabrication with robotic systems.
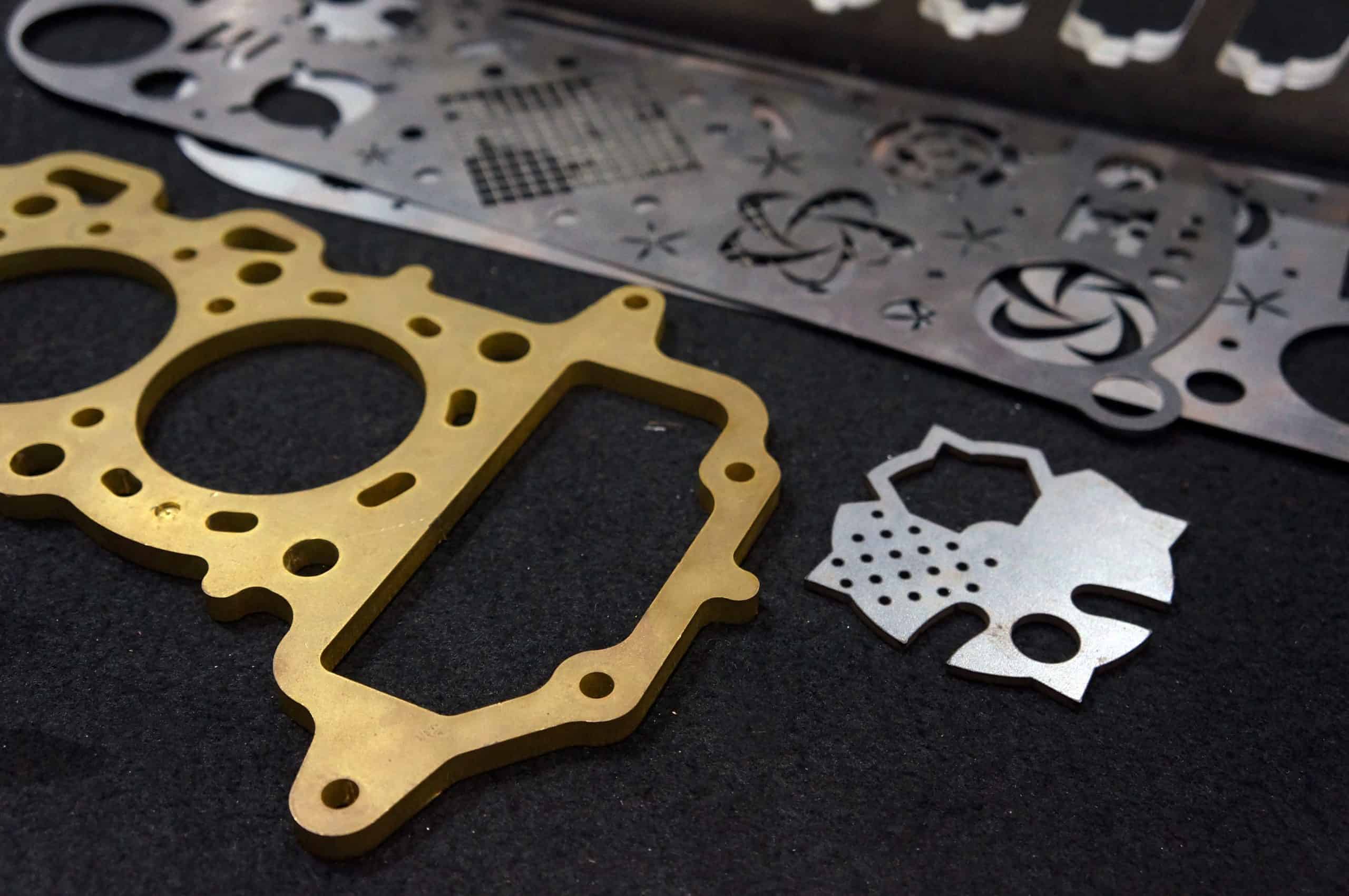
Different materials require different cutting techniques.
Get an Instant and Competitive Sheet Metal Fabrication Manufacturing Quote
- Easily find the custom part manufacturer your project requires
- Get instant and competitive quotes on your RFQs
- All uploaded files are securely stored on MFG and only released to manufacturers at your discretion
Note: MFG does not service the textile, jewelry, or clothing industry.

Request a Quote
Have part files ready?
Submit an RFQ in 2 easy steps.
Step 1
Upload your part file below.
Drag and drop a file here or click to upload
Oops! The file size needs to be less than 500 MB. Please upload a small file.
All files are protected by the MFG Standard NDA and are securely stored on MFG.
Step 2
Just a few extra details.
Your Contact Information
Let them know how to contact you.
All information is transmitted and stored securely. We will never sell your information.
Congratulations!
We have received your RFQ! Once accepted, we will contact you.
Hi! Did you know you can keep track of this RFQ in your MFG Community account?
How does the fabrication of sheet metal occur?
Sheet metal fabrication begins with design, followed by production and assembly of the finished product. Metal fabrication occurs in either a continuous process for higher-demand products, or a batch process for custom designs.
Phase 1:
Design
Sheet metal fabrication usually begins with a customer request, initiated during design and product development. This process requires a variety of software tools that enable visualization of the product via computer-aided design (CAD). Seeing the product firsthand saves time,resources, and increases profitability. Additionally, any tweaks can be made prior to manufacturing.
Phase 2:
Production Process Programming
Production operations follow a specific sequence, beginning with approval of the final design. Machinery involved in fabrication is programmed according to the design specifications, and parts are meticulously mapped out on the metal sheet, ensuring optimal material usage. Any necessary adjustments are made to maximize the yield of parts from a single sheet.
Phase 3:
Sheet Metal Cutting
Metallic materials are very tough in nature. Cutting through them often requires heavy duty instruments like a saw, or lasers, which are the current industrial standard for precision in metal cutting. Leading companies are known for prioritizing use of the best tools to manufacture their products.
Phase 4:
Product Assembly
After sheet metal components have been cut, they must be molded and combined to produce the finished product. A few processes used in assembly include:
- Punching: Metallic sheets often have to be shaped to produce forms such as cylinders, or to create a space for perforations where bolts can be attached. Special CNC punching machines impact the metal, making required indentations and holes. Scrap metals that are formed during this process are often collected and recycled.
- Bending: Bending tools are used to create angular indentations on a metal sheet. This process is known more technically as CNC folding, conducted either manually or automatically, depending on the resources available.
- Welding: Metallic components are either bolted together or welded. The welding process relies on heat energy from a torch to melt and fuse two independent metals together. Various welding techniques can be chosen, depending on the material being worked.
Phase 5:
Product Finishing
After all the metallic components have been prepared, they must be interlocked according to the predetermined design. Metallic products can form the framework of a system such as a car. Components such as the engine, cushioned seats and electrical components are added and the entire product is secured. Product testing is conducted after the cosmetic finishes are complete.
Powder Coating: Metals are prone to corrosion if they are exposed to the elements. For this reason, they must be thoroughly cleaned and treated. Powder coating is an electrolytic process used to deposit a protective coating onto the metal. Afterward, any additional coatings such as paint can be applied.
How Sheet Metal fabrication optimizes manufacturing
Sheet metal fabrication optimizes manufacturing by enabling a smooth transition from design to actual product. Precision manufacturing is now the emerging industrial standard, and with the integration of computers and programmable machines, the exact sequence, material input, and final product output can be predicted. Gone are the days of having to machine a product through trial and error. Computer-aided design provides a clear visual of the expected result, with machines executing each step in production precisely.
The advantages of these tools include faster turnaround time, more efficient processes, and better scheduling capabilities of manufacturers. High standards of quality are maintained if robots are used to produce products, versus humans. Since machines never tire, paused only for maintenance, operations are continuous, with identical output at each stage. The process is truly a win-win for the customer and the manufacturer.
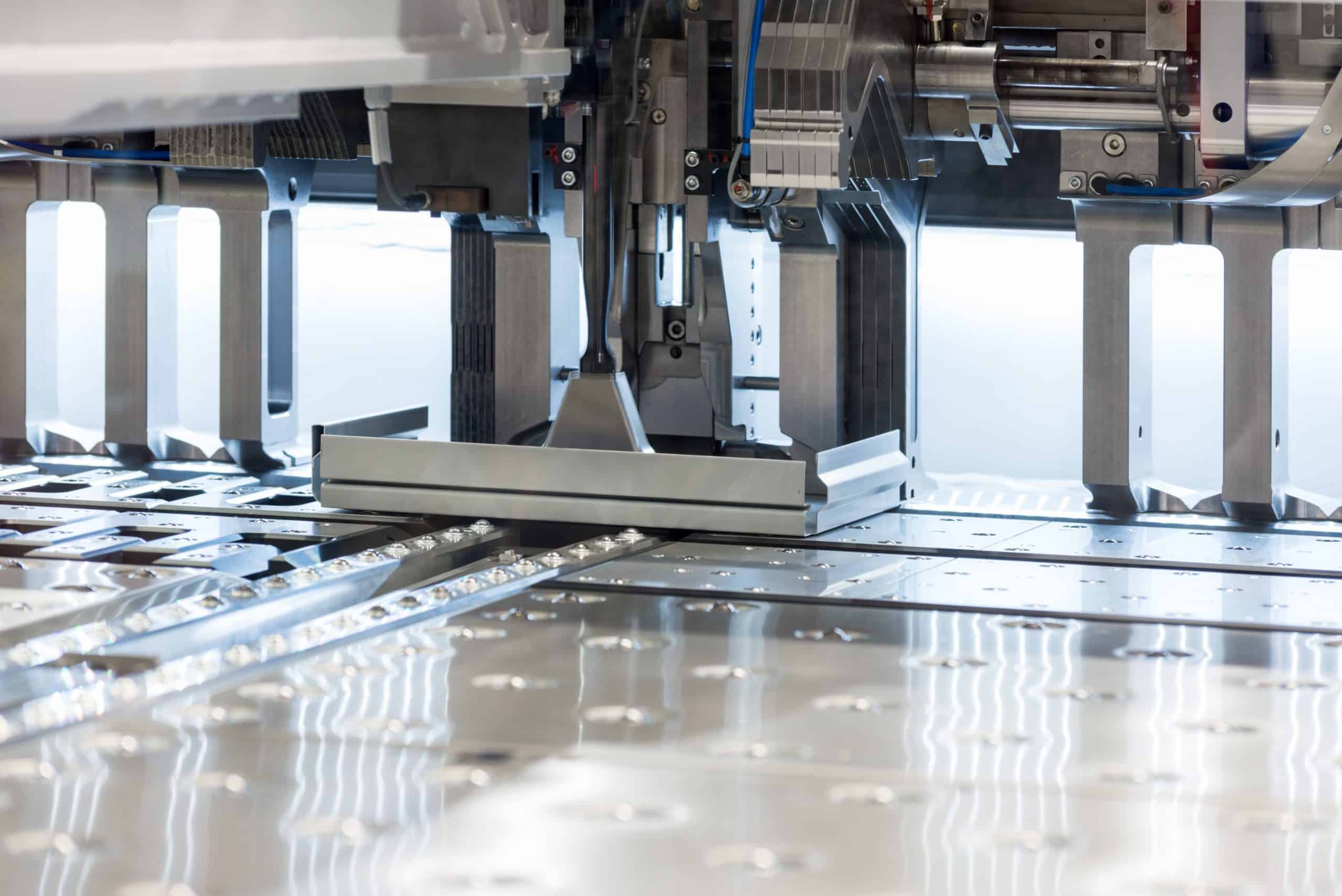
Bending tools are used to create angular indentations on a metal sheet.