What Is Custom Manufacturing and What Are its Top Benefits?
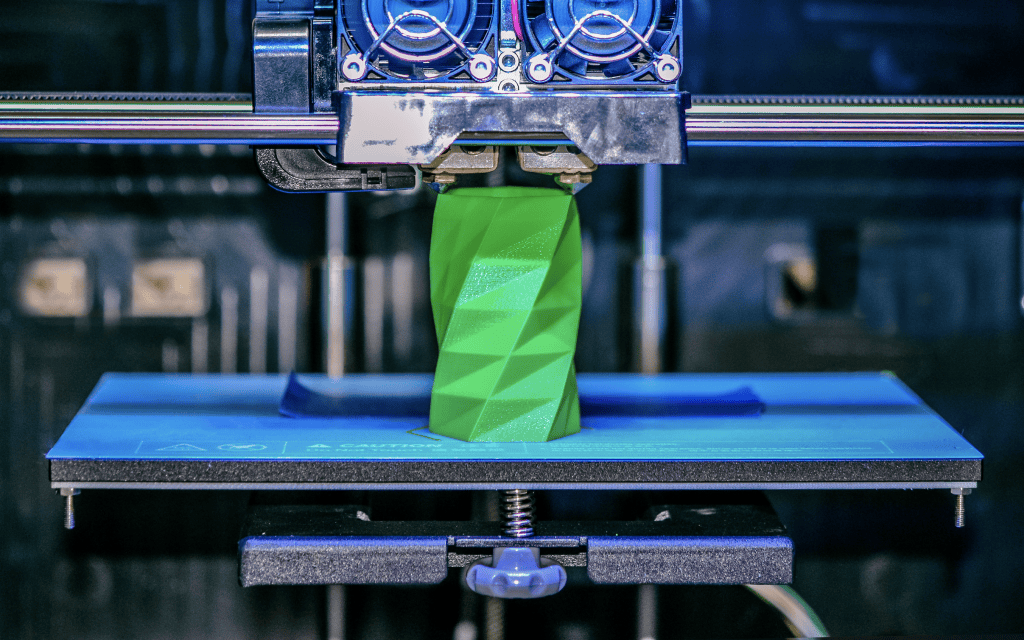
Demand for customized and personalized products is higher than ever in many industries. Yet the century-old mass production model struggles to satisfy this growing appetite for tailored goods, leaving manufacturers unable to meet the needs of discerning customers.
The solution is a collaborative process that allows manufacturers to work hand-in-hand with customers to build products to their specific requirements.
Read on to discover what custom manufacturing is, learn how to shift production to a more flexible model, and find out how you can successfully meet your customers’ evolving expectations.
What is Custom Manufacturing?
Custom manufacturing is the process of designing and manufacturing products tailored to meet your unique specifications. In contrast to mass production, this method requires a highly personalized, hands-on approach and involves close collaboration between the customer and the manufacturer. Orders can range from one-off prototypes to large-scale production.
Custom manufacturing is often used to produce specialized products such as aerospace parts, medical devices, and military equipment. Due to its highly skilled nature, most custom manufacturers focus on catering to niche product categories or providing particular manufacturing processes.
Custom Manufacturing vs Mass Production
The limitless customization options of custom manufacturing contrast sharply with the highly standardized processes of mass production.
Custom manufacturing can guarantee much higher-quality products than mass production can achieve as product features and quality assurance checkpoints are tailored to your needs and priorities rather than pre-set specifications. Your production capacity may be lower than with mass manufacturing, but the tradeoff allows you to avoid carrying excess inventory.
Additionally, as you’re working closely with the engineers, design changes are more straightforward compared to reconfiguring entire assembly lines. However, the hands-on approach of custom fabrication can involve higher labor costs per unit. You won’t achieve the same economies of scale possible with mass production runs, but the profit opportunity in serving customer niches often outweighs raw efficiency.
How Does Custom Manufacturing Work?
The custom manufacturing process is iterative and involves extensive collaboration to translate your into a tangible product. The process can be broken down into the following key stages:
Design
The first step in custom manufacturing is design. Your company, or a design partner, will need to create CAD models according to your exact needs and specifications. The complexity of your product will determine the timeline and can range from hours for simple items to months for more intricate projects.
It is helpful to follow Design for Manufacturing principles to ensure that the final product is high quality and matches your vision.
Request for Quote
After your designs are ready, submit a Request For Quote (RFQ) on an online manufacturing marketplace. This RFQ should include all the information potential manufacturers might require to provide an accurate quote such as:
- 2D Drawings
- 3D Model Files
- Material Specifications
- Part Quantities
- Tolerances
The RFQ should also specify the manufacturing techniques that will be used such as injection molding or CNC machining.
Initial Meeting
The marketplace then connects you with qualified manufacturing partners to arrange a meeting to discuss your vision in more detail, whether via email, video call, or in person. You can assess your candidate to determine if it will be a positive supplier relationship.
Prototyping
Next, a physical prototype is constructed to allow you to evaluate the design. Prototyping is crucial for the early identification and rectification of any problems.
Production
Once the prototype meets with your approval, the process shifts to the production phase which could involve a range of techniques including injection molding, 3D printing, metal fabrication, or CNC machining. Multiple production test runs may be necessary to ensure the product meets your quality standards.
Testing and Quality Control
Compared to mass manufacturing, you can be more hands-on in the testing and quality control phases. To ensure your satisfaction, you can work closely with the manufacturers throughout material checks, capacity tests, certifications, and other touchpoints.
Scaling Up Production
Finally, once signed off, your custom production line can scale efficiently to handle larger batch orders. At this point, you can even leverage standardized mass production methods to balance customization with cost-efficiency.
DESHAZO struggled to meet its extreme quality requirements within delivery timelines when it relied solely on its internal manufacturing capacity. Using the MFG manufacturing marketplace, DESHAZO easily found suppliers capable of quick-turn, precision machining tailored to their specifications. The robotics company speedily increased production capacity without capital investment, letting it scale rapidly.
What Are the Top 4 Benefits of Custom Manufacturing?
Adopting a custom manufacturing model offers many crucial advantages compared to traditional mass production. Here are the most significant gains you can make by leveraging this approach:
1. Lowers Costs
Custom manufacturing allows products to be made to suit specific budgets compared to the limited options of mass production pricing. No minimum orders are required, risk is reduced, and overall costs can be lower than mass production while generating less material waste.
2. Speeds up Production
With fewer production steps, custom manufacturing eliminates wait times for standardized components. This facilitates quicker access to production and reduced lead times to market.
3. Offers Flexibility and Unique Specifications
By removing the limitations of mass production, custom manufacturing permits enhanced personalization and construction according to your exact specifications.
4. Improves Quality Control
Working directly with engineers allows higher scrutiny during the build process. This enables immediate identification and rectification of defects – which is beneficial for companies producing high-quality niche products.
The US Army turned to the MFG Marketplace when it needed to find manufacturers with the capacity to quickly produce machined aluminum housings. Its RFQ was answered with multiple quotes from skilled shops that delivered quick turnaround on these customized parts of the required quality and cost.
What Are the Different Types of Custom Manufacturing Options?
When discussing custom production techniques, it’s important to note that they mainly fall into subtractive and additive manufacturing categories:
Subtractive Manufacturing
Subtractive techniques start with a solid block of material. Portions are removed by cutting or shaping until the desired object is created. Unlike other processes, subtractive techniques offer quicker, less labor-intensive production and smoothly surfaced parts without additional grinding or polishing. Subtractive manufacturing can also tackle complex geometries that other methods can’t.
Common subtractive approaches include:
- CNC Machining
- Plasma Cutting
- Water Jet Cutting
Additive Manufacturing
This builds objects layer-by-layer straight from 3D CAD models. This facilitates the refinement and customization of designs without requiring expensive molds. Additive systems can also produce multiple unique products using the same core equipment. Standard additive fabrication technologies include:
- 3D Printing
- Multi-Jet Fusion
- Stereolithography
Choose MFG to Source the Best Custom Manufacturer for Your Product
Custom manufacturing is your best option when you need specialized, high-quality, or unique products made to order. It’s a flexible process that promises improved cost efficiency, personalized design and quality control, and superior agility over mass production.
Seeing this promise realized hinges on connecting with the right manufacturing partner. MFG provides an interactive hub to streamline your search thanks to:
Simplified Supplier Discovery
MFG’s online marketplace directly connects over 26,000 manufacturers and 75,000 buyers worldwide.
Efficient Collaboration
Global manufacturer listings mean expanded options, while direct order management enables smooth communication. Buyers average 4+ quotes from US fabricators.
Enhanced Features
Advanced search filters, quick RFQ posting, peer reviews, SEO profiles, and intelligent RFQ routing matching projects to optimal partners.
Learn more about how you can leverage the MFG platform to achieve transformative business results via strategic custom manufacturing relationships.
Fortunately, MFG offers a one-stop shop to simplify your search. MFG’s comprehensive manufacturer directory provides instant access to all the details you need to consider, such as facility size, capabilities, and certifications. Our directory also provides reviews and ratings from previous customers to help guide your selection.
MFG streamlines your selection process further by enabling the creation of RFQs (Request for Quote) directly within the platform, significantly reducing the steps involved in outsourcing to a manufacturer. Register now to find your ideal outsourcing partner.