Lessons on Design for Manufacturing from ETHO CEO & Founder Dave Fustino
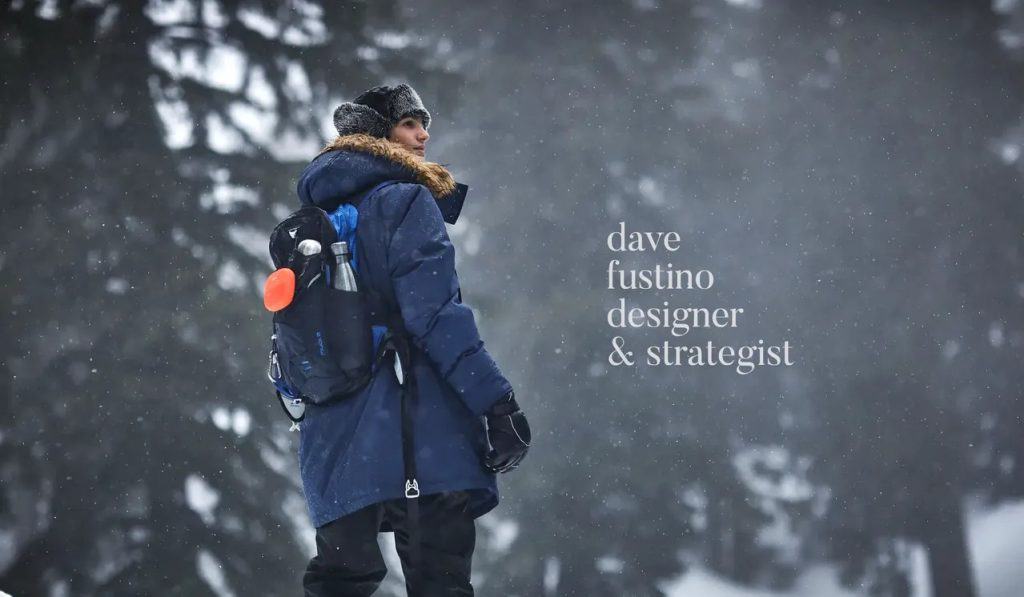
MFG was recently joined by Dave Fustino, CEO and founder of ETHO, for a conversation on streamlining product development for mass manufacturing. Dave gave insights on how to transform an idea into a tangible product design and prepare it for manufacturing, tips for how to communicate and collaborate with manufacturing partners, and gave a look into his own approach to creating innovative and functional products that are ready for production.
Dave is an industrial designer based in Boston who has worked with brands such as Bose, Philips, and Aira, and has designed speakers, appliances, lighting, wearables, and more. We asked him to provide advice to other designers and people interested in inventing products – here are his suggestions.
Top Tips for Making Designs a Reality
Dave has three top tips for making designs a reality:
- Prototyping
- Good material knowledge
- Supplier engagement
Prototyping comes first in importance as a step in the process for Dave. As he put it, “Creating functional and visceral prototypes is very critical to improving a designs manufacturability”. Testing, learning, and gathering feedback all comes from the prototype phase of a design. Secondly, Dave emphasized having a good material knowledge base. Knowing material properties and needs can make a huge difference in the end product’s function. Finally, Dave mentioned how important supplier engagement is. For independent designers, having a good supplier base and good coordination and communication with them will help identify areas of improvement needed in a product before it goes to market.
Choosing the Right Supplier
Choosing the right supplier or manufacturer is essential. Most important is the ability for the manufacturer to demonstrate their capabilities through previous examples of their work that are similar to your desired product. Also important is the quality, timing, and pricing of the supplier. Dave looks for a supplier that can deliver the desired quantity and quality of parts, move forward on an agreed upon time table for production, and do it all at a reasonable price that works for the client’s budget.
Working with a Supplier During Manufacturing
Dave underlines the importance of “being receptive to being collaborative in the part development and refinement throughout the process” to “improve efficiency and overall quality”. Supplier feedback on the part and design is very important, as is maintaining a strong relationship with the manufacturer. That relationship is built over time and allows a designer to go back time and time again. For Dave, maintaining that relationship looks like scheduling commitments, establishing timelines for deliverables and expectations, clear tolerance and requirements for supplier and clients, and regular communication to assess the entire process and agreed upon terms.
General Advice for Aspiring Designers
Bringing a product to life is “quite the process and very involved” especially in the current competitive market. Dave recommends leveraging your insights if you notice a clear opportunity in a broad market. This allows addressing unmet needs with a new product. When pursuing an innovation, Dave says to “be diligent and test often”. Maintain being true to your audience and remembering who the design is for and the target audience to create a great product. As Dave says, “A great product truly eliminates problems and removes obstacles for the customers that it resonates with”.
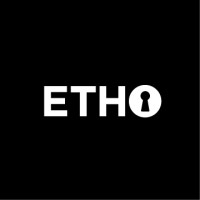
Dave’s company, ETHO, focuses on sustainable design. He believes that moving the industry towards more responsibly manufactured and distributed parts is more important than ever. Dave strives to have his parts make as little an environmental impact as possible on a global scale. You can check out this website at etho.design and Dave himself can be reached at his website, davefustino.com.
If you want to hear Dave Fustino’s conversation with Staci Matt for Shapeways Manufacturing Week, you can listen here.