What Is Sheet Metal Laser Cutting?
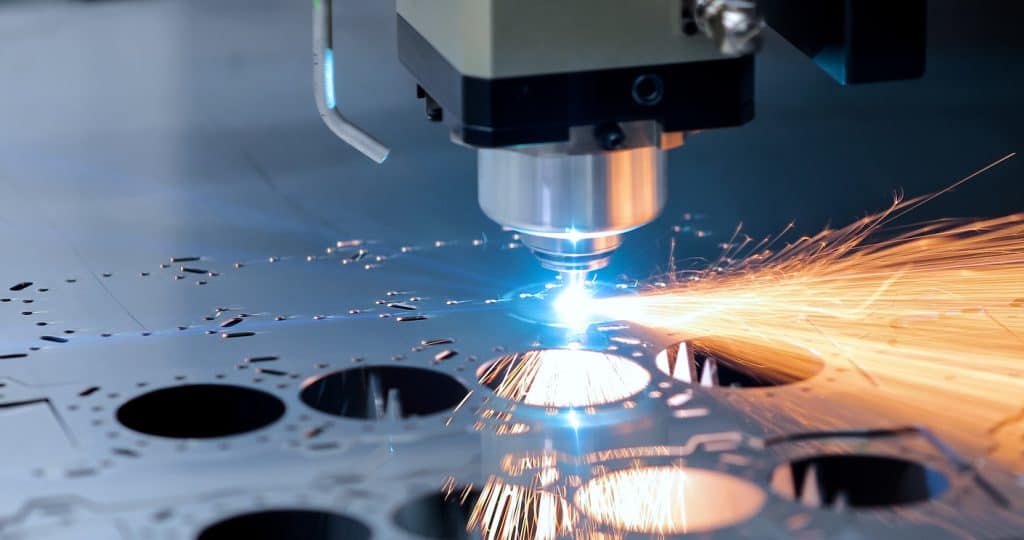
Manufacturers transforming raw materials into finished products rely heavily on cutting processes. Over time, cutting techniques have advanced, introducing new methods that provide enhanced precision, efficiency, and flexibility.
Among these innovations, laser cutting of sheet metal has emerged as a revolutionary technology, garnering widespread adoption within the industry. This cutting-edge approach has empowered manufacturers to overcome the limitations associated with conventional sheet metal cutting methods.
Discover the intricacies of sheet metal laser cutting, the key advantages driving its popularity, and how to find a trusted laser cutting expert.
What Is Sheet Metal Laser Cutting?
In sheet metal laser cutting, a Computer Numerical Control (CNC) system directs a concentrated laser beam across the metal. This beam “subtracts” material by melting, burning, or vaporizing along the programmed path.
The focused, high-energy laser cleanly slices through the metal, while the CNC targeting allows for the creation of intricate shapes at a fast pace. To carry out this process, 2D designs are uploaded to the laser cutting machine. It then uses the vector image data to trace the parts on the sheet material. The result? Burr-free components with smooth edges and precise cuts, meeting tight tolerances with accuracy.
What Are the Types of Sheet Metal Laser Cutting?
There are three main types of laser technologies used to cut sheet metal. Each has its particular set of capabilities suited to different materials and applications. Here is a detailed breakdown:
1. CO2 Lasers
Carbon dioxide (CO2) lasers utilize a gas mixture medium to produce a laser beam that can be concentrated intensely enough to slice through thick, durable metal sheets. CO2 lasers generate a wavelength of light that is readily absorbed by most metals, allowing them to effectively cut through over 1 inch of carbon steel, stainless steel, aluminum, and more. With the capability to penetrate thicker and stronger metals, CO2 laser cutting provides a highly adaptable and rugged fabrication solution.
2. Fiber Lasers
Fiber laser cutters amplify light through an optical fiber core to create a potent yet precise beam. This allows for tight focus and small spot sizes, resulting in fast, smooth cutting action and superior edge quality. Fiber laser cutters are used on medium-gauge metals like brass and copper. They strike an optimal balance between cutting speed, precision, and operating costs.
3. Crystal Lasers
Crystal laser resonators emit light in selected bands perfect for lower power density cutting. The crystalline solid-state lasing medium enables stable continuous wave beam production.
What Are the Top 5 Benefits of Sheet Metal Laser Cutting?
Let’s take a look at how sheet metal laser cutting can transform the design for manufacturing process thanks to the following features:
1. High Versatility
Laser cutters provide exceptional versatility in materials and thicknesses. Fiber, CO2, and crystal lasers can collectively cut steel, aluminum, brass, copper, and more from thin gauges up to over an inch thickness. No other single process matches this cutting breadth.
2. Design Flexibility
Since the focused laser beam can follow virtually any path, you gain immense creative freedom over part geometries. Laser cutting can quickly generate complex holes, curves, cutouts, and precision features that would otherwise require extensive machining setups.
3. Minimal Material Waste
The laser’s narrow cut width or kerf means little material is lost during cutting. Flame cutting and mechanical processes like punching or stamping produce wider kerfs and more waste. Greater sheet usage efficiency means lower materials costs.
4. High Precision
Laser cutting provides exceptionally repeatable precision, even for intricate shapes. The CNC targeting allows accuracy down to thousandths of an inch to meet your tightest tolerances. No tool wear issues exist unlike with mechanical cutting.
5. Automation & Integration Capabilities
Laser cutters directly interface with CAD software and readily integrate with automated production and 3D printing processes. This enables consistent lights-out manufacturing and further quality gains, substantially improving overall efficiency.
What Are the Challenges of Sheet Metal Laser Cutting?
While laser cutting delivers immense fabrication benefits, there are some inherent challenges to consider when learning how to cut sheet metal with lasers. These include material thickness limitations, cost of maintenance, and environmental considerations.
Here is a detailed breakdown of the challenges:
1. Material Thickness Limitations
Laser cutting does face physical limits in the thickness it can penetrate for metals like steel and aluminum. Thicker materials require higher-powered lasers, slower cut speeds, and multiple passes, and also incur risk from heat buildup. Going beyond 2.75-inch thickness typically requires exploring alternative cutting methods.
2. Cost of Maintenance
Industrial laser cutters require a high initial outlay to acquire. Specialized personnel are also needed to operate and perform preventative maintenance. Consumable costs like replacement lenses and laser gas refills also add up over years of use.
3. Environmental Considerations
The high energy density of laser cutting generates noxious fumes, metal particulates, and gases during use. If not adequately controlled, these pose risks to human health and the environment. Proper fume extraction systems, along with gas, water, and particulate filters are essential to mitigate the hazards.
What Is the Sheet Metal Laser Cutting Process?
There are three main laser-cutting techniques: Fusion, sublimation, and flame.
Let’s look at how each method works:
1. Laser Beam Fusion Cutting
Fusion cutting uses the laser’s intense heat to melt the sheet metal locally into a molten pool along the beam path. High-pressure assist gas, commonly oxygen or nitrogen, then blows the molten metal out of the cut to achieve total separation while shielding the lenses. Fusion cutting is widely used for mild and stainless steel sheets.
2. Laser Beam Sublimation Cutting
Sublimation cutting avoids melting and relies on the laser’s energy to turn sheet metal directly from a solid into a gas. A pressurized assist gas jet blows away the vaporized material, offering a clean, narrow cut within the heat-affected zone.
3. Laser Beam Flame Cutting
This method involves combining a laser beam with oxygen. The laser preheats a path to kindle burning while the oxygen stream fans the flames. This method is faster than fusion or sublimation cutting but can leave rough edges on thicker metals.
What Industries Use Sheet Metal Laser Cutting?
The following industries use sheet metal laser cutting processes to fabricate high-precision metal parts and products:
1. Automotive
Automakers and parts suppliers use laser-cut sheet metal to manufacture lighter, stronger brackets, braces, enclosures, panels, exhaust components, and other vehicular structures from steel and aluminum. Precision cutting minimizes waste while allowing more complex part designs.
2. Aerospace
The aerospace sector employs laser cutting to produce robust and lightweight aircraft skin panels, engine housings, bulkheads, wings, turbines, and other structures from titanium, Inconel, stainless steel, and aluminum alloys.
3. Electronics
Electronics manufacturers use the precision of laser cutting to produce integrated outer structures, shields, mounting racks, internal frames, and heat sinks for electronic devices and computing hardware.
4. Medical
Medical device producers use sheet metal laser cutting technology to reliably create bone plates, replacement joints, and other healthcare equipment from biocompatible metals that need to meet high-quality standards.
How MFG Provides Access to Specialized Sheet Metal Laser Cutting
Sheet metal laser cutting techniques offer some unmatched advantages to manufacturers. However, as we have covered, adopting sheet metal laser cutting in-house requires significant capital investments in equipment, facilities, personnel, and more.
Luckily, you can turn to MFG’s manufacturing platform to find a skilled manufacturer rather than directly taking on these costs and complexities.
MFG offers instant access to a global network of pre-vetted manufacturers. Simply submit an RFQ detailing your design requirements, and MFG’s proprietary matching algorithms will instantly connect you with qualified partners.
Submit your request for a quote today to find a manufacturer offering cost-competitive quotes for sheet metal laser cutting.