CNC Machining vs Plastic Injection Molding
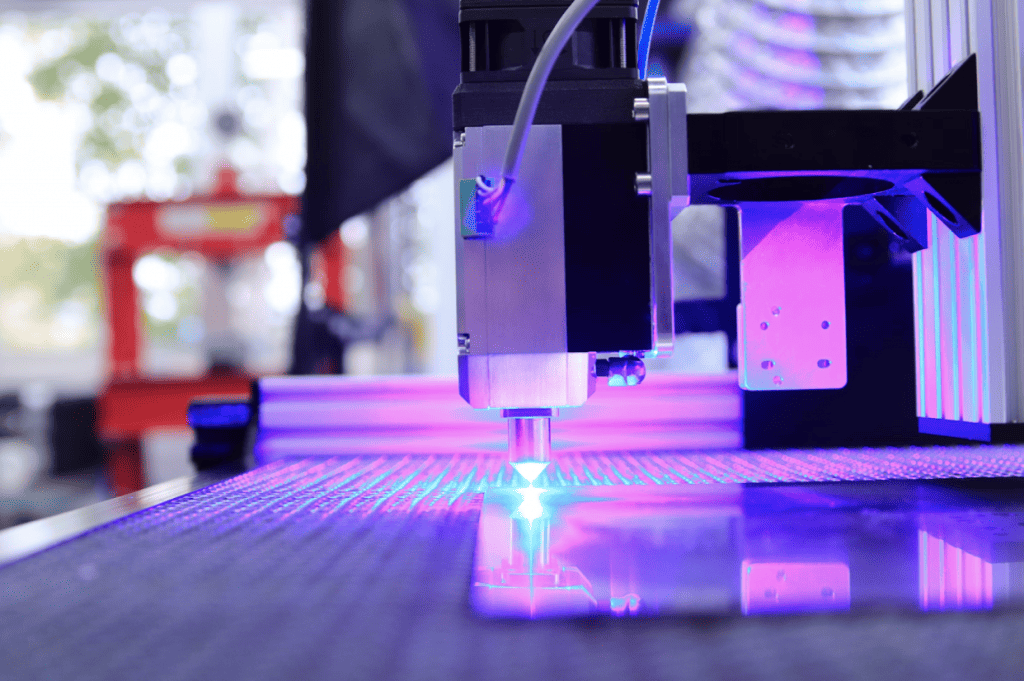
From prototyping to mass production, your choice of manufacturing technique plays a central role in determining your time to market as well as the quality and cost-effectiveness of your final product. CNC machining and plastic injection molding both allow you to make parts quickly and accurately, but these processes are quite distinct from each other and have varying use cases. So, it’s vital to consider which manufacturing process can best deliver the results you need. Read on to discover all you need to know about CNC Machining vs Plastic Injection Molding and find out which third option you should also consider.
What is CNC Machining?
A computer numerical control (CNC) machine is an automated manufacturing tool used for cutting, shaping, and producing high-precision items from a range of materials. CNC computers use pre-programmed sequences of commands to control the movement of cutting tools and other machinery and perform tasks such as milling, turning, drilling, routing, and grinding, among others. Various industries, such as aerospace, automotive, and industrial equipment manufacturing use CNC machining to produce complex high-quality parts and components with extreme precision.
What is Plastic Injection Molding?
This manufacturing process produces parts and components by injecting plastic material into a mold cavity under high pressure. Once the plastic cools and solidifies within the mold, it takes on the shape of the cavity creating the desired object. Plastic injection molding is highly versatile and can be used to produce complex shapes with precise dimensions and tight tolerances. It is used in various industries, including automotive, aerospace, consumer goods, medical devices, and electronics manufacturing to produce a wide range of parts and products.
Comparing CNC Machining vs Plastic Injection Molding
Sometimes the choice between CNC Machining vs plastic injection molding is clear, for example, if you need to work with metal, you don’t even need to consider injection molding. However, when it comes to plastic, either option may be a viable choice, and here’s where understanding the pros and cons of each can be useful. Let’s take a closer look at the advantages and disadvantages of CNC machining vs injection molding.
CNC Machining Pros
- CNC machines can use a wide variety of materials, including metal, wood, plastic, expanded polystyrene foams, ceramic, stone, glass, and rubber.
- Their modular design and standardized components make them easy to customize for your changing needs.
- CNC machines offer the ability to use precise, small-diameter tools for greater accuracy and tighter tolerances.
- Automated processes and high-speed cutting capabilities mean they can manufacture parts quickly and efficiently.
CNC Machining Cons
- CNC machines have a high purchase price, require regular maintenance, and can be very expensive to repair if something goes wrong. To offset this cost, you can outsource manufacturing to a CNC machinist shop.
- While they automate and speed up the manufacturing process, CNC machines do require devoting some additional resources to training employees in their use and programming. This is another con that can be mitigated through outsourcing.
Plastic Injection Molding Pros
- Plastic injection molding can produce a large volume of parts very rapidly and the plastic pieces solidify quickly.
- Injection molded parts require very little in the way of cleanup and can be shipped almost immediately.
- For large quantities, plastic injection molding can usually offer the lowest price per part.
Plastic Injection Molding Cons
- Reworking plastic injection molded parts can be quite difficult due to the nature of the molding process and the potential for damage during reprocessing.
- This technique involves high upfront costs, primarily due to the expense of tooling and mold creation.
- Injection molded parts can be prone to surface flaws caused by factors such as mold imperfections, material impurities, or processing conditions.
- Plastic injection molding can only produce plastic objects, if you need to use other materials, this process is not an option.
When the U.S. Army needed to find manufacturers that specialized in making machined aluminum housings it turned to the MFG Marketplace and expanded its pool of manufacturers capable of producing precision parts to its demanding specifications in short timeframes.
An Alternative to CNC Machining and Plastic Injection Molding
When choosing how to produce your parts or components, it’s not simply a choice between CNC machining vs injection molding, there’s a third option to consider. The best fit for your needs might be 3D printing.
As an additive manufacturing process, 3D printing offers distinct advantages such as its ability to handle complex geometries and uniquely customized parts with minimal tooling requirements. It allows for rapid prototyping and an iterative design process, making it suitable for low-volume production or one-off parts. 3D printing can use a variety of materials, and is well-suited for producing lightweight, intricate parts. It is also relatively inexpensive; both the materials used for 3D printing and the initial set-up costs of the machines are lower than CNC machines or injection molding.
However, there are some limitations to 3D printing that you should take into account. 3D-printed parts are usually less durable than items made with other types of manufacturing and require more finishing than the outputs of CNC machining or injection molding. While 3D printed parts can be made to tight tolerances, they may not always match the level of precision achieved through CNC machining or injection molding. This is especially true for filament-based machines (as opposed to resin 3D printers) that need careful calibration to ensure that all 3 axes are tightly controlled.
Trust MFG to Help You Find the Right Manufacturer
Ultimately, CNC machining, injection molding, and 3D printing each have their part to play in manufacturing and your choice depends on your specific use case and factors such as material requirements, desired quantity, and budget considerations.
With MFG, you have access to all the benefits of plastic injection molding, CNC machining, and 3D printing without having to invest in expensive equipment or retraining your employees. MFG can quickly connect you with thousands of verified custom manufacturers and our customer ratings and reviews help you select a partner with the specialized skills and equipment to make any part you need.
If you are looking for a manufacturer, MFG’s manufacturer directory is just a click away.