Improving Cost Savings for Your Business
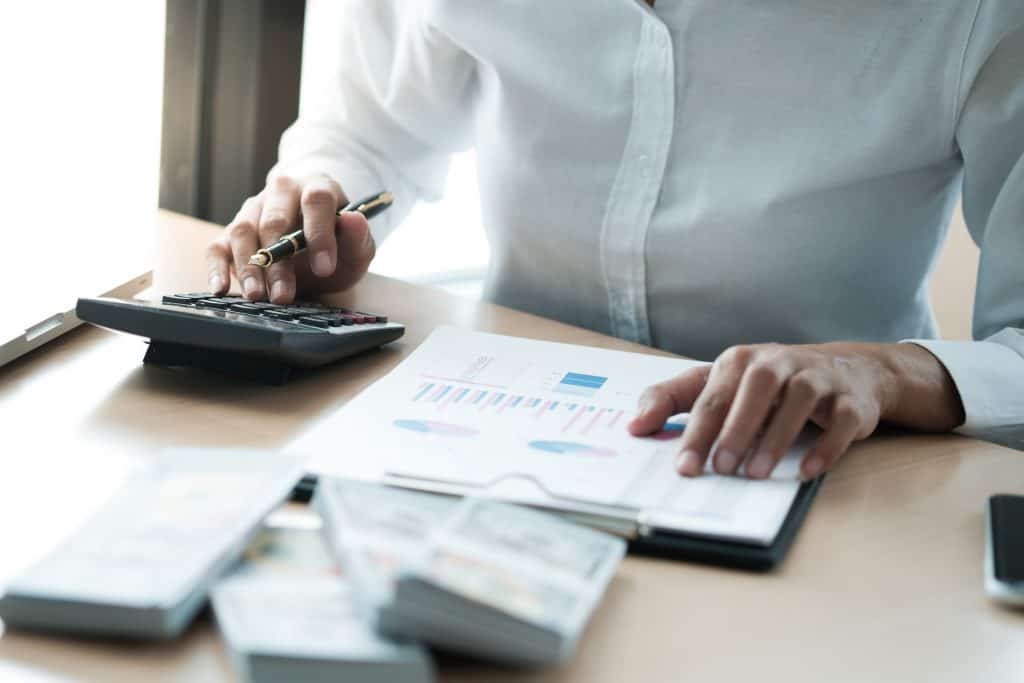
Recent rising costs and inflation are affecting businesses everywhere, in every industry. If you’re in the business of producing and manufacturing physical products, you know how much more expensive the entire process has become, from material sourcing to labor costs. Global events, supply chain issues, and a variety of other factors have influenced the growing expenses of running a business and have forced business owners to re-evaluate their spending. 2024 is expected to bring some slightly lower rates of inflation, but there are actions you can take in the meantime to improve cost savings for your business and increase your return.
Maintaining a profitable business with high-quality products when the economy isn’t at its best is doable; it just takes a few adjustments. Being willing to implement changes into your business model, increasing communication both internally and externally, creating and maintaining a budget, and exploring new partnerships are just some of the ways to reach your goals. In this blog post, we’ll explore more ways you can improve cost savings for your business, and how MFG can help.
8 Ways to Reduce Manufacturing Costs
1. Visualize Your Goals: Short-, Mid-, and Long-Term
One of the first things you can do to increase your business’s profitability is to get out of only thinking about the here and now and start focusing on your goals for the future. These can be broken out into short-, mid-, and long-term goals and can apply to any facet of your business, from income to brand image. After establishing realistic targets, you can then set a roadmap to reach them. An investment can seem like a great move right now, but with a zoomed-out lens, might not actually be of the most benefit to your company. For example, choosing a manufacturer who can quickly turn around your product for cheap might seem like a great idea when you’re low on cash, but if you want to build a reputation for having quality products, will it help with your long-term goals?
2. Aggregate Tasks and Save Time
Every task you complete needs time and money (and time is money), so are there any functional tasks that can be combined to save on both those resources? Maintaining the quality of products and services should remain important, but if two tasks can be compiled and done together without taking a loss on quality, then this action will save you or an employee time, which can then be allocated towards other tasks or even just save on labor costs.
MFG is a great way to save time during the sourcing process. MFG allows you to get quotes from multiple manufacturers at the same time by submitting a single request for a quote, so you don’t have to manually send quotes out to individual manufacturers. You can also compare all the quotes on one screen, saving you even more time. These competitive quotes will ensure you get the best price while you’re at work on something else.
3. Use Outsourcing, Freelance, and Contract Work
To continue to reduce costs in-house, both for materials and labor, turn to outsourcing, freelance, and contract work. Do you need some content written or promotional materials designed and don’t have the budget to hire a copywriter and/or graphic designer? Sites like Upwork are free to use and feature freelancers who specialize in all manners of work and content creation and can be hired for specific projects. Hiring a contract worker for a short-term job is another way to get work done without breaking the bank.
In addition to being able to hire on an as-needed basis, contractors also cost less because they do not have benefits that need to be paid out. Their hourly rates may be higher, but they still ultimately save you cash. While full-time employees can be a long-term goal, finding great freelancers can be a great way to get your business the help it needs on a smaller budget.
4. Reduce Manual Work In-House
Manufacturing products in-house requires a lot of upfront costs that can take years to pay off. You need to rent a bigger space, purchase machines, source raw materials, and hire staff that can keep everything running smoothly. Instead of piling on these costs, consider working with an established manufacturer to produce your custom parts.
Signing up as a buyer on MFG.com is free, as is posting a request for a quote (RFQ). A quote through an outside manufacturer found on MFG could be significantly cheaper than if you produced in-house, but will still give you the quality you desire. Read reviews, communicate with the manufacturers, and feel confident that you’re getting the price and quality you deserve.
5. Designing Products Specific to Cost
Saving money in the production stage includes finding an affordable manufacturer, but also ensuring the production of your products aligns with your budget. Sticking to a set budget for your company means that clear communication needs to occur with your manufacturer on design and production. You know the vision for your product, but maybe there’s a material or process it could be produced in that helps reduce the cost per unit. Speak with your manufacturer about creating your products specific to a cost.
Set a specific budget for your products and communicate with your suppliers on the desired cost per unit to stay on track with that budget. A restricted budget doesn’t mean you have to lose product quality either, MFG offers a variety of manufacturers producing high-quality work at a competitive price!
6. Increase Production and Administrative Efficiency
Another place you can save costs within your businesses lies in streamlining production and administrative efficiency. A variety of tools are available for use, many of which offer free packages for small teams or starter packages for larger businesses. Organizational software like Asana or Trello allows you to easily delegate tasks, prioritize work, and communicate with team members. Giving your employees a clear roadmap of upcoming projects and what needs prioritization will facilitate a more streamlined business where time and money do not go to waste.
7. Increase Employee Productivity
Employee productivity is essential to cost savings for your business. If your current employees are productive, there is no need for additional hiring or spending on your part. Productivity can be increased in part through administrative efficiencies, but also through company culture and employee support. Forbes found that employees who are measured by their work outcome instead of activity are happier and more likely to be productive towards company goals. Brainstorm ways you can make your employees feel important in your company culture, how you can support them, and how to encourage continued good work.
8. Facilitate Marketing Partnerships
Part of creating and maintaining a successful company with lower costs is facilitating partnerships and building local networks. Finding the right partnerships is essential; look for other companies in similar industries with customer bases akin to yours but with enough of a difference that you’re not in competition. Teaming up with adjacent companies for marketing events or referrals, for example, could bring you both profits that wouldn’t have been financially feasible alone. Developing a local network and relationships with all manners of businesses can also facilitate the growth of your business to reach your long-term established goals.
There are many internal factors that go into running a quality and profitable business and many external factors that can make the profitable part of that equation difficult. Supply chain issues, rising costs, and inflation all make increasing cost savings for your business difficult, but not impossible. With tips like those listed above and tools like MFG, you can save on costs for your business and strive to reach your company goals.